Optimalizace plánů preventivní údržby na základě hodnocení rizika
Tento článek se zabývá problematikou optimalizace plánů preventivní údržby na základě hodnocení rizika. Cílem je návrh jednotného systému, který pojme optimalizaci údržby zařízení jako celek a docílí lepších výsledků než při aplikaci samostatných moderních metod údržby (RCM – Reliability Centered Maintenance, RBI – Risk Based Inspection, SIFpro – Safety Instrumented Function).
1. Úvod
V současné době se převážná většina společností při údržbě svých zařízení řídí tzv. programem (řádem) preventivní údržby. V tomto programu je přesně stanoveno, v jakých intervalech a v jakém rozsahu se u zařízení mají provádět jednotlivé stupně údržby (prohlídka, běžná údržba, revize, generální údržba apod.). [11, 14] Tyto intervaly byly stanoveny především podle doporučení výrobce, a to na základě dlouhodobých zkušeností s provozem zařízení, případně na základě určitých optimalizačních výpočtů či zkušeností, které respektovaly nejen samotnou poruchovost zařízení, ale také náklady spojené s údržbou a opravou zařízení. Nedílnou součástí údržby jsou také legislativní požadavky na kontrolu (revizi), které ovlivňují odstavení zařízení. [1]
Cílem údržby je uchovávat zařízení v takovém stavu, aby jeho pohotovost byla co nejvyšší, aby nedocházelo ke zbytečným poruchám, během nichž zařízení není schopno plnit svou funkci. Běžné systémy údržby přistupují ke každému zařízení daného druhu stejně, bez ohledu na to, kde v podniku je umístěno, jaké přenáší zatížení, jaké je napojení na další výrobu apod. Není respektována tzv. důležitost zařízení. [10] Důležitostí zařízení se rozumí významnost zařízení z hlediska dopadu jeho poruchy na provoz celého podniku. Metody tuto skutečnost respektují a poskytují tedy mnohem efektivnější programy údržby, než doposud používané postupy.
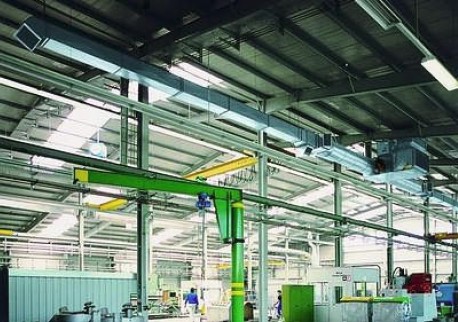
Obr. 1 Větrání, vytápění a klimatizace rozsáhlých prostor [15]
Účinné a efektivní programy údržby jsou nutné pro splnění požadavků, například pro bezpečnost, kvalitu, nízké provozní náklady aj. S velkým počtem výrobních jednotek v rámci společnosti, může být obtížné stanovení priorit činností údržby. Použití moderních metod údržby k hodnocení rizika přispívá k identifikaci závažných rizik v rámci společnosti, které v kombinaci s různými strategiemi údržby usnadní stanovení priorit úkolů. Výstupy získané prostřednictvím moderních metod údržby jsou pak využívány k upravování nebo předefinování existujících programů údržby.
V současné době lze spatřovat velkou podobnost mezi výrobním zařízením menšího průmyslového podniku a větráním, vytápěním a klimatizací rozsáhlým prostor jako jsou velké stavební objekty nebo administrativní budovy, kde jsou rozsáhlé a složité strojovny zajišťující patřičné klima pro odpovídající práci strojů i pracovníků. Na obrázku číslo 1 je příklad systému větrání a odvětrávání haly o ploše 5200 m2. V této hale je 8 teplovzdušných agregátů (s výkonem více jak 175 kW) a 48 vysoce výkonných odsávacích střešních ventilátorů. [15]
2. Metodika měření
V kontextu údržby, inspekce a měřicích přístrojů má každá z moderních metod údržby svůj specifický účel při optimalizaci údržbářských činností, ale přesto jsou tyto metody určitým způsobem propojeny:
RCM (Reliability Centered Maintenance – Údržba zaměřená na bezporuchovost)
RCM představuje strategii pro optimalizaci údržbářských prací, která se snaží zabránit vyšší nákladovosti nebo nižší pohotovosti zařízení. RCM se v zásadě zabývá všemi způsoby poruch, které nejsou pokryty metodami SIFpro a RBI. Metodu lze aplikovat na tvorbu údržbářských plánů pro strojní objekty jako jsou zařízení strojní (zejména rotační stroje), stavby, elektrická zařízení a měřicí přístroje. [6] Konečným výsledkem je základ plánu preventivní údržby a seznam doporučených zlepšení. RCM může být rovněž použita při vypracovávání projektu jako pomoc při výběru zařízení, co se týče optimální spolehlivosti a nákladů na dobu životnosti, a rovněž může být použita při vypracování základu plánu údržby.
RBI (Risk Based Inspection – Inspekce na základě rizika)
RBI představuje strategii pro optimalizaci inspekčních a údržbářských prací, která se snaží předejít možné ztrátě úniku média. [2, 3] Metoda RBI se používá k řízení integrity tlakové obálky. Je to objektivní nástroj pro určení rozsahu inspekčních prací pro plánované výrobní zarážky a určení přesných částí stacionárního zařízení, které mají být otevřeny kvůli inspekci. Metoda se rovněž používá pro určení inspekcí za provozu mimo zarážku. Podobným způsobem jako RCM lze RBI rovněž použít během vypracovávání projektů jako pomoc při volbě konstrukčních materiálů – opět co se týče optimální spolehlivosti a nákladů na dobu životnosti zařízení. V rámci RBI jsou zvažovány všechny takové způsoby poruch, které ovlivňují tlakovou integritu zařízení a potrubních vedení. Ostatní způsoby poruch stacionárních zařízení, jako úsady, by měly být analyzovány v rámci RCM.
SIFpro (Safety Instrumented Function – Bezpečnostní přístrojové funkce)
SIFpro představuje strategii pro optimalizaci plánu testovacích intervalů jednotlivých regulačních smyček [5]. SIFpro pokrývá nahodilé bezpečné a nebezpečné poruchy jistících přístrojů, včetně alarmů. Jedná se o přesně vymezenou oblast v rámci měřicích přístrojů. [4] Měřicí přístroje, které jsou zahrnuty pod SIFpro patří i pod metodu RCM, ale z jiného pohledu rizika a údržby. Rovněž způsoby poruch jistících přístrojů, které jsou časově závislé, by měly být analyzovány s pomocí RCM. Cílem je dospět k údržbářským činnostem, které zabrání výskytu poruch, které by vyústily do skutečných bezpečných nebo nebezpečných poruch.
3. Návrh systému „řízení rizika a spolehlivosti“ (ŘRS) pro implementaci metody RCM, RBI a SIFpro
Metody na optimalizaci preventivní údržby už existují řadu let a jejich aplikací se zabývá řada společností. Přesto zatím není moc náznaků, že by byla snaha implementovat tyto metody jako celek a byla pojata optimalizace preventivní údržby na všechna zařízení, která se na výrobě podílejí. Každá ze tří základních metod může být aplikována samostatně a v jakémkoliv preferovaném pořadí. Co se týče pořadí metod, je třeba je přizpůsobit konkrétnímu případu. Například lze provést RCM až poté, co se aplikovalo RBI, aby před studií RCM byl již definován nejdelší možný cyklus zarážek, který vychází z hodnocení integrity zařízení. Nicméně je třeba přiznat, že implementace všech tří metod (nebo alespoň dvou z nich) poskytne větší přínosy, než aplikace jedné.
Každá metoda (RCM, RBI a SIFpro) se soustředí na specifickou oblast, čímž poskytne účinný nástroj při generování úkolů/prací údržby. Hlavním přínosem tohoto návrhu je sladěný a strukturovaný přístup spočívající v těchto výstupech:
- Metody poskytují konzistentní a uniformní způsob hodnocení rizika. Toto napomůže vyjasnění struktury organizace a rovněž usnadní například jednání s úřady.
- Snižuje se pracovní zatížení jednotlivých odborností, jelikož data a informace z jedné metody mohou být použity v druhé metodě.
- Zlepšuje se synergie jednotlivých základních metod, výsledkem jsou přínosy kompletní studie ŘRS, které budou větší než součet přínosů jednotlivých metod.
- Vytvoří se lepší porozumění a schopnosti aplikovat činnosti vycházející z hodnocení rizika v rámci personálu z různých oblastí jedné provozní jednotky. [7, 8, 9]
Rozsah aplikace jednotlivých metod na výrobní zařízení
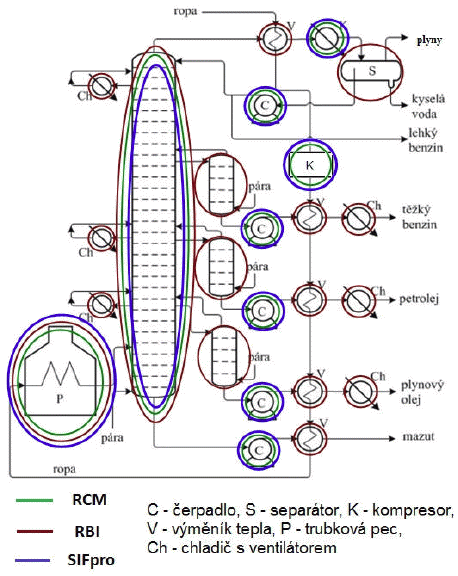
Obr. 2 Rozsah působnosti jednotlivých metod na výrobní jednotku (schéma atmosférické destilace ropy)
Výrobní jednotky, v sekci výroby, jsou často označovány jako podniky, závody či továrny, které pomocí výrobního zařízení mění materiály nebo substance na nové produkty. Všechny tři metody jsou zaměřeny na výrobní zařízení, které se podílí na výrobě (jednotlivé stroje, součásti, potrubí, měřicí přístroje či aparáty se vzájemným vztahem). [6]
Jestliže by se porovnával rozsah jednotlivých metod, nelze vždy jednoznačně říci, která metoda je nejrozsáhlejší, a tudíž si zasluhuje největší pozornost, vždy záleží na struktuře zařízení každé výrobní společnosti.
V chemickém průmyslu (obr. 2) má největší rozsah metoda RCM, která obsáhne většinu výrobních zařízení. Je to dáno tím, že metoda se zabývá převážně strojními zařízeními (zejména rotační stroje), které jsou hojně zastoupeny ve zpracovatelském průmyslu. Dále lze této metody využít pro stavební, elektrická zařízení, filtry a měřicí přístroje. [12, 13]
Metoda RBI obsáhne veškerá tlaková a potrubní zařízení. Konkrétně do metody patří kolony, reaktory, výměníky, chladiče, potrubí aj. Do metody patří mnoho zařízení, která podléhají tzv. mandatorní údržbě. [2, 8]
Metoda SIFpro pokrývá poruchy jistících přístrojů, včetně alarmů. [4]
Pokud by metody byly aplikovány separátně, tak nepojmou veškerá zařízení, která se na výrobě podílí. Tím, že se metody navzájem prolínají, neznamená, že se provádí stejná analýza – každá z metod má svůj postup na hodnocení preventivní údržby na základě rizika.
Struktura navrhovaného procesu implementace
Organizovaný a společný přístup ke zlepšení preventivní údržby by měl být cílem každé výrobní společnosti. Často ale mohou vznikat problémy se zaváděním těchto metod, protože to představuje významnou změnu pro organizaci, a to nejenom v oblasti údržby, ale i v ovlivnění výroby či začlenění managementu do procesu. Některé z důvodů, proč se metody nedaří zavést, jsou technické povahy, ale většina problémů je manažerských a organizačních.
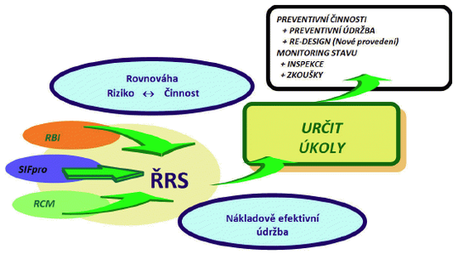
Obr. 3 Proces systému ŘRS (Řízení rizika a spolehlivosti)
Rozhodovací procesy vycházející z hodnocení rizika se stávají stále více důležitými nástroji pro řízení činností, procesů, produktů a služeb společností. Navrhovaný systém ŘRS (obr. 3) je jedním z rizik vycházejících nástrojů pro určování úkolů/prací preventivní údržby, inspekce a monitoringu, které jsou nutné k dosažení nezbytné pohotovosti zařízení, a to při vynaložení optimálního úsilí.
Každá metoda se soustředí na specifickou oblast, čímž se poskytne maximální efektivnost při generování údržbářských činností. Hlavní přínos při zavedení tohoto systému je sladěný a strukturovaný proces. Celý proces ŘRS je kombinací analýzy a provádění preventivních prací. Analýza ŘRS představuje týmovou práci prováděnou skupinou příslušných odborníků z provozu, údržby, procesní technologie, oblasti materiálů a koroze, inspekce, bezpečnosti, elektro a instrumentace.
Fáze ŘRS
Navržený systém je kvůli větší přehlednosti a jednoduššímu pochopení rozdělen do pěti fází (obr. 4), které jsou dále rozděleny do jednotlivých dílčích bloků. Každá fáze je chápána jako proces, který se skládá z dílčích činností, které na sebe navzájem navazují či se prolínají. Vstupy a výstupy jednotlivých fází tvoří data, informace, formuláře, postupy, doporučení aj., které jsou nedílnou součástí procesu.
První fáze pojednává převážně o možnostech implementace metod do procesu údržby ve společnosti. Zabývá se shromažďováním dat a informací formou auditu, dále školením zaměstnanců i managementu. Tyto činnosti následně pomohou správně nastavit proces implementace, aby mohl být úspěšný.
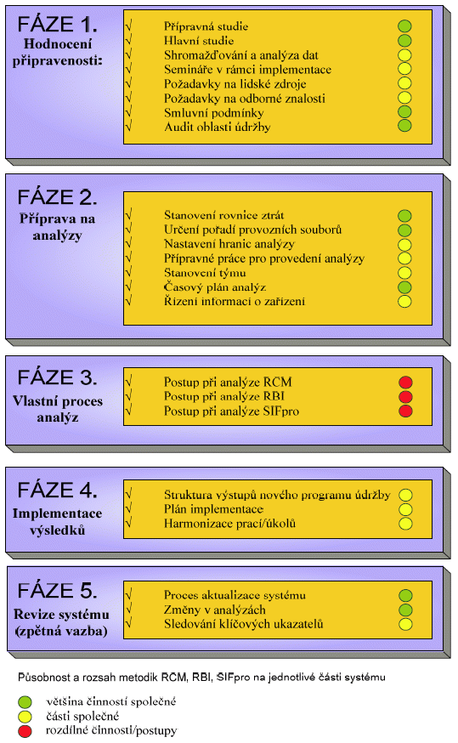
Obr. 4 Diagram návrhu procesu ŘRS (Řízení rizika a spolehlivosti)
Ve druhé fázi se připravují konkrétně všechna potřebná data k tomu, aby analýzy metod mohly probíhat ve schváleném plánu. Příprava zahrnuje nejenom sběr a tvorbu samotných dat, ale i koordinaci specialistů, zaměstnanců, kteří se na analýzách podílejí.
Třetí fáze je vlastní proces analýz, který probíhá podle stanoveného postupu, aby byl zachován ucelený pohled na analyzované provozní jednotky a výsledky byly v jednotné podobě.
Čtvrtá fáze se zaobírá implementací a sestavením jednotlivých výstupů z analýz, které je potřeba skloubit do jednotného balíku dat pro přesun do informačního systému údržby. Dále je důležité zkombinovat nové intervaly údržby či inspekce do plánů tak, aby zohlednily plánované odstávky provozů, legislativní požadavky či generální opravy.
Poslední pátá fáze řeší aktualizaci implementovaného systému v případě změn, které se během provozu vyskytnou. Poukazuje na oblasti, ve kterých případné změny mohou vést k transformaci provedených analýz a hodnocení.
Návrh systému ŘRS byl aplikován na výrobní jednotce – hydrogenační rafinace plynového oleje. Tato jednotka slouží k rafinaci surového plynového oleje ve vodíkové atmosféře cirkulačního plynu na příslušném hydrogenačním katalyzátoru. Zařízení, na které byly analýzy aplikovány, se skládá převážně z kompresorů, čerpadel, výměníků, chladičů, ventilátorů, reaktorů, kolon, potrubních systémů, jistících přístrojů aj.
Porovnáním s jinou výrobní jednotkou (s podobným rozsahem zařízením), kde byly implementovány tyto metody převážně separátně, došlo k úspoře času implementace metod v řádu 30 %. Zahrnuje to převážně časy zaměstnanců provozu, specialistů a techniků údržby, kteří se na procesu podílejí. Největší podíl na zefektivnění procesu má fáze č. 2, kde se nejvíce prolínají jednotlivé metody, a lze využívat informace z jedné metody pro metodu druhou. Díky tomu dochází k výraznější úspoře času přípravy.
Po zavedení systému údržby, který je řízen a optimalizován na základě rizika se očekává zlepšení v několika oblastech údržby, a to zejména v procesu plánování preventivní údržby a inspekce. Zefektivnění tohoto procesu sebou přináší nejenom snížení nákladů, ale i další nehmotné výhody:
- snížení pracovního zatížení, jelikož informace a data z jedné metody mohou být použity ve druhé,
- stanovení strategie údržby zařízení založené na hodnocení rizika,
- optimální spolehlivost a pohotovost zařízení,
- zajištění technické integrity zařízení,
- snížení nákladů na údržbu a zachování požadované pohotovosti a spolehlivost zařízení,
- splnění měnících se požadavků HSE (zdravotně bezpečnostní a environmentální oblasti) a legislativním požadavkům,
- jednotná databáze pro registraci údajů o údržbě, inspekci a jištění,
- usnadnění procesu zpětné vazby pro trvalé zlepšování,
- aktualizovaný registr majetku,
- jeden zdroj pro plány a rozhodnutí v oblasti údržby inspekce a jištění,
- zlepšení procesu nakládání s náhradními díly,
- postupné vytvoření databáze spolehlivosti,
- řádné zdokumentování majetku, obnovení dokumentace,
- centralizace pracovních postupů údržby zařízení,
- širší zapojení provozních pracovníků do oblasti preventivní údržby,
- prostředí multidisciplinárních týmů navozuje atmosféru užší spolupráce mezi odděleními údržby, technologie a provozu.
4. Závěr
Při návrhu systému, který jde napříč organizačními strukturami, liniemi pravomocí a zasahuje do mnoha zavedených procesů ve společnosti, není ho jednoduché začlenit do procesu bez překážek. Potíže, se kterými se implementace systému ŘRS do provozní praxe může setkat, jsou dány mnoha faktory, které lze rozdělit do několika základních oblastí:
- vysoké nároky na datové vstupy,
- nároky na informační vstupy,
- kvalita analytické činnosti,
- organizace údržby,
- vytvoření podmínek a podpora managementu.
Bez dostupnosti nezbytných datových vstupů (kde „nezbytných“ je často synonymem pro „rozsáhlých a detailních“) nelze přistoupit k analytické činnosti. Jedná se o tyto třídy dat u seznamu majetku až na úroveň komponentů, ke kterým jsou následně vztahovány ekonomické a provozní údaje, vstupy do rovnic výrobních ztrát, dokumentace (technologická schémata, výkresová dokumentace), náklady na údržbu (ceny komponent a náhradních dílů, náklady na jednotlivé typy údržby apod.), paměť údržby (záznamy o provozu, údržbě a evidenci poruch zařízení).
Nároky na informační vstupy jsou stejně důležité jako datové vstupy, kvalita analytické práce při jejich nedostatku je zásadně negativně ovlivněna. Převážně se jedná se o popisy funkcí zařízení a postupů procesu (výroby), způsob provozování zařízení za normálních a mimořádných situací či návaznosti a vzájemné funkční závislosti technických zařízení.
Kvalita analytické činnosti představuje jádro procesu ŘRS. S využitím metod a technik oboru spolehlivosti, diagnostiky a hodnocení rizik jsou datové a informační vstupy transformovány do nákladově efektivních strategií údržby. Pro tyto analytické činnosti je zapotřebí vytvořit multiprofesní tým (více týmů) provozních a údržbářských pracovníků doplněných specialisty na spolehlivost, korozi či bezpečnostní systémy a podobně.
Výsledky analytické činnosti musí být uspořádány do programů údržby, což vyžaduje schopnost nasazení efektivních postupů a jejich dokonalou organizaci v programu údržby. Prosazení objektivně pozitivních změn indikovaných výsledky analýz může být v praxi nejobtížnějším článkem postupu.
Vytvoření podmínek a podpora managementu souvisí s organizací údržby a je zcela klíčová, protože implementace systému ŘRS je složitý a náročný proces, jehož rozběh se ani při optimálních podmínkách nevyhne komplikacím, které mohou vyústit ve zpoždění proti plánovanému harmonogramu. Vždy vyžaduje koncentraci finančních a lidských zdrojů. Po implementaci se tyto procesy musí stát trvalou součástí provozní praxe (se všemi klady), jinak se nepodaří získat všechny pozitivní výsledky, které systém nabízí.
I když jsou tyto faktory obecně platné, mají nestejnou váhu, která je zpravidla závislá na organizační a odborné úrovni managementu, kde se systém ŘRS zavádí. Pro úspěšnou implementaci metod řízení rizika a spolehlivosti je naprosto zásadní vytvoření potřebných podmínek a vysoká podpora vrcholového managementu těmto postupům. Tato podpora je nutná, protože při zavádění ŘRS jdou implementační procesy napříč celou společností. Nedostatečná úroveň vstupních dat či speciálních znalostí z oboru spolehlivosti, diagnostiky či korozní problematiky, není v jednotlivých fázích a okamžicích realizace tak rozhodující, protože postupně lze data shromáždit a znalosti předat.
Hlavním smyslem aplikování systému ŘRS nejsou úspory (ty jsou vedlejším produktem), ale stanovení řádné strategie údržby zařízení provedené na základě analytické metody s vyhodnocením rizika, a tím i přesnější směřování finančních prostředků, tam kde je to z pohledu rizikovosti nejdůležitější.
Poděkování
Příspěvek byl vytvořen za podpory grantového projektu č. ČZU 31190/1312/3122 "Vliv biopaliva a provozních parametrů na kouřivost motoru.
Literatura
- [1] Anthony M. Smith and Glenn R. Hinchcliffe: RCM – Gateway to World Class Maintenance, Elsevier, 2003 ISBN: 0-7506-7461-X
- [2] API RP 580, Risk-Based Inspection, Second Edition, American Petroleum Institute / 01-Nov-2009 / 96 pages
- [3] API 510, Pressure Vessel Inspection Code: Maintenance Inspection, Rating, Repair, and Alteration – Includes Addenda 1, 2, 3 and 4 (1999, 2000, 2001, 2003), Edition: 8th Edition, American Petroleum Institute / 01-Jun-1997 / 54 pages
- [4] ČSN EN 61511: 2005, Funkční bezpečnost – Bezpečnostní přístrojové systémy pro sektor průmyslových procesů.
- [5] ČSN EN 61508-2:2002, Funkční bezpečnost elektrických/elektronických/programovatelných elektronických systémů souvisejících s bezpečností.
- [6] ČSN IEC 60300- 3-11. Management spolehlivosti – Část 3–11: Návod k použití – Údržba zaměřená na bezporuchovost, 2010
- [7] Interní dokument České Rafinérie a.s: Pracovní postup údržby – Údržba zaměřená na bezporuchovost (RCM), (3. úroveň dokumentace, první vydání, 2010)
- [8] Interní dokument České Rafinérie a.s: Pracovní postup údržby – Inspekce na základě ocenění rizika (RBI), (3. úroveň dokumentace, první vydání, 2010)
- [9] Interní dokument České Rafinérie a.s: Pracovní postup údržby – Bezpečnostní instrumentální funkce na základě rizika (SIFpro) (3. úroveň dokumentace, první vydání, 2010)
- [10] Moubray, J.: Reliability-centred Maintenance. Butterworth-Heinemann, 1997, ISBN 0-8311-3146-2
- [11] Mykiska, A.: Bezpečnost a spolehlivost technických systémů. 1. vydání. Praha: České vysoké učení technické v Praze, 2006, 206 s. Učební texty ČVUT v Praze. Fakulta strojní. ISBN 80-01-02868-2.
- [12] SAE JA1011: 2009, Evaluation Criteria for Reliability-Centered Maintenance (RCM) Processes, 12 pages
- [13] SAE JA1012: 2002, A Guide to the Reliability-Centered Maintenance (RCM) Standard, 57 pages
- [14] Mayer, K., Pexa, M., Aleš, Z., Weinfurtner, L.: Interval technické diagnostiky při měření čerpadel, Časopis – TZB-info, Ročník 13, číslo 48, Topinfo s.r.o., Praha, ISSN 1801-4399, 2011, s. 1–8.
- [15] Nunner, G.H.M., Kubík, J: RHEINLAND – vytápěcí a větrací systém velkých prostor, Časopis – TZB-info, Ročník 3, číslo 43, Topinfo s.r.o., Praha, ISSN 1801-4399, 2001, s. 1–3.
Zaměření příspěvku
Odborný příspěvek se zaměřuje na problematiku údržby zařízení, především na vytváření samotného programu údržby. V úvodní části jsou přehledně představeny metody řízení Údržby na základě rizik plynoucÍch ze způsobů poruch technických systému a zároveň je poukázáno na slabá místa při izolované aplikaci pouze jedné z metod. Příspěvek se zaměřuje především na metody RCM, RBI, SIFpro. Na základě provedené rešerše je navržen strukturovaný proces zohledňující všechny tři uvedené metody, nazvaný jako ŘRS – Řízení rizika a spolehlivosti, jehož předností je (kromě jiných benefitů) finanční a časová úspora dosažená vhodnou organizací celého optimalizačniho procesu.
Závěr
Téma údržby je aktuální problematikou, což dokazuje zájem průmyslových objektů o optimalizaci plánů údržby a tím snížení celkových nákladů souvisejících s provozováním technických zařízení. Příspěvek „optimalizace plánů preventivní ÚdrŽby na základě hodnocení rizika“ navrhuje na základě dostatečně provedené rešerše inovativní způsob řízení údržby. Příspěvek hodnotím po stránce odborné i formální na velmi dobré úrovni a doporučuji ho k publikování v odborném časopise.
V Liberci dne 20. 6. 2012 Ing. Jaroslav Zajíček, Ph.D.
This article is focused on plan optimization issues of preventive maintenance based on risk assessment. The aim is to propose a cohesive system layout which involves the maintenance optimisation as a whole and achieve better results compare to simple applying the individual methods. This system is divided into five fundamental phases which are consequently following one after another and guarantee the order and structure of the process. Every phase consist of individual sections which thoroughly describe particular execution and procedures. The proposed system should help readers to obtain sufficient information in order to understand the different parts of the system and enable them to make their own opinion on synergy of systematic methodology which deals with optimization of maintenance. All these aspects are very important in practice due to the complexity of most ventilation, heating and air conditioning systems.